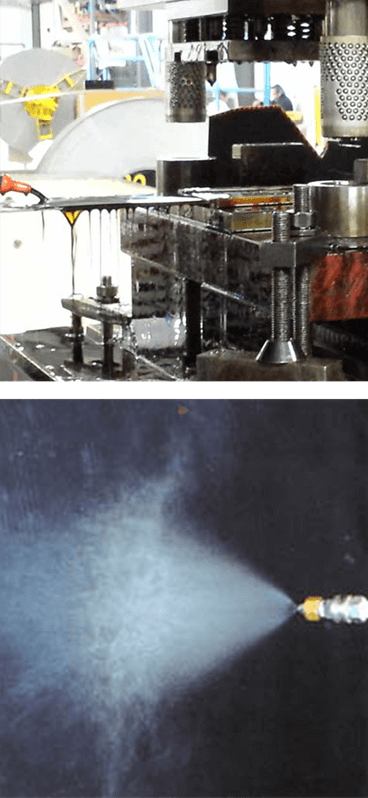
Where spray, roller or “through the die” application methods are employed—care is taken to either more consistently apply and/or pinpoint more critical areas where tooling and parts require more protection. In the case of flooding, application is far more random and inconsistent. The goal is, after all, to lubricate the parts and tooling rather than the entire press bed, part and scrap conveyors and shop floors.
Consideration should be given to the type or class of stamping lubricant used when optimizing lubricant application. Some types of fluids are more easily/efficiently applied using some methods over others. Product viscosity, surface wetting/spreadability, and the presence of certain types of EP/AW additives can dramatically impact the ability of lubricant delivery to parts. In general, oil-based fluids will spray differently than water-based fluids. Products that are emulsions or dispersions can have significantly different stability than the true solutions formed by synthetic, water-based products. IRMCO’s heavy duty, oil-free stamping lubricants are designed for minimal quantity application—eliminating the need for flooding.
Consider also that by minimizing the volume of lubricant applied to parts/tooling, parts are easier to inspect for quality, are typically drier in storage and will improve plant cleanliness and operator safety by not weeping out of part hoppers and presses onto floors and production equipment.